Accurate as-built documentation is invaluable for construction projects, and new digital technologies help it evolve.
Because most construction projects undergo at least some minor changes during construction, design drawings are typically updated to document the final project conditions. Changes might include location adjustments of project elements, additional work or different materials substituted for originally specified items.
For example, a door may be moved on a building project. A drainage structure on a roadway project may be relocated to avoid underground utilities. A different pump may be installed in a manufacturing facility as a cost- or energy-saving measure.
Construction industry professionals have used various approaches to document as-built conditions of projects. Many projects have employed the redline approach, where design or construction plans are marked up (usually in red) to show the finished conditions of a project. These are often prepared by the construction contractor and referred to as “as-built drawings.”
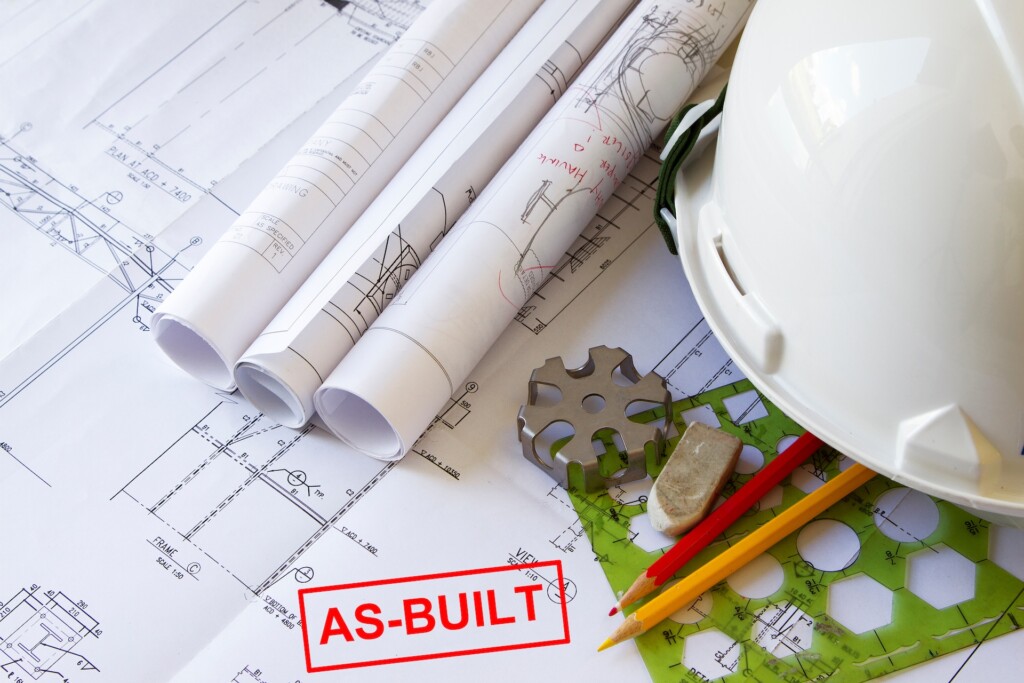
Some organizations make a distinction between as-built drawings and record drawings. The American Society of Civil Engineers, for example, in its policy statement 290 – Post-construction drawings of civil engineering projects says: “Record drawings are used to verify substantial compliance with the design documents for inventory, asset management, maintenance needs, and for record keeping purposes. Record drawings are distinct from ‘as-builts’ because they should be and often are sealed by the engineer or surveyor of record that provided oversight during construction. As-builts are typically completed by the contractor and are without a seal.”
Other organizations, such as the American Institute of Architects and the Construction Management Association, offer additional guidelines on record drawings and other types of as-built documentation. Governmental agencies may have additional requirements and contract terms regarding such documents.
Regardless of terminology, as-built documentation is valuable in documenting final project conditions. The availability of accurate information can help project owners manage their facilities, guide future renovations and provide reliable records for various parties with interests in the project. For example, a new project located adjacent to a recently completed project will often benefit from accurate as-built information.
Digital technology changes landscape
With digital technologies such as computer-aided design (CAD) and building information modeling (BIM) used on a growing number of projects, the approach to developing as-built documents has been evolving. Instead of marking up paper plans, many project teams use electronic redlining tools to update drawings or directly update digital models to reflect field changes.
Field information gathered with electronic tools such as laser scanners and drone-based imagery has also changed as-built documentation processes. Instead of taking manual measurements, teams can use laser scans or digital imagery to establish actual locations of project elements and compare them with design locations.
Digital twins — virtual representations of real-world entities — have added another twist. Many projects employing digital twins call for updating the digital models on an ongoing basis to reflect physical conditions, making the redline markup unnecessary or a bit of an outlier. In addition to laser scanning data, additional data from sensors, digital photographs and other sources can be used to document as-built conditions. Instead of redlining drawings, teams often rely on drawing revision records to track changes.
With updated and synchronized digital twins, owners and construction teams can make more informed operation and maintenance decisions. Models can be used to track asset performance and predict future behavior via simulations and mathematical modeling. Instead of guessing when pumps or motors might need replacement, actual data can be used to help make those decisions. Updated digital models can also provide access to a wide variety of data, such as part numbers, material details, shop drawings and photos, often accessible via mobile devices.
Immersive technologies such as virtual reality (VR) and augmented reality (AR) can also be used to view project updates. If a door was moved in a building, an interested team member can view the change remotely using VR/AR technology.
Other developing technologies, such as artificial intelligence (AI), may also impact how as-built information is collected and documented. AI tools can guide the collection and processing of drone-based data and create 3D models representing site conditions. These models can be used as a basis for creating as-built documents or as a reference for comparing the design and the actual conditions.
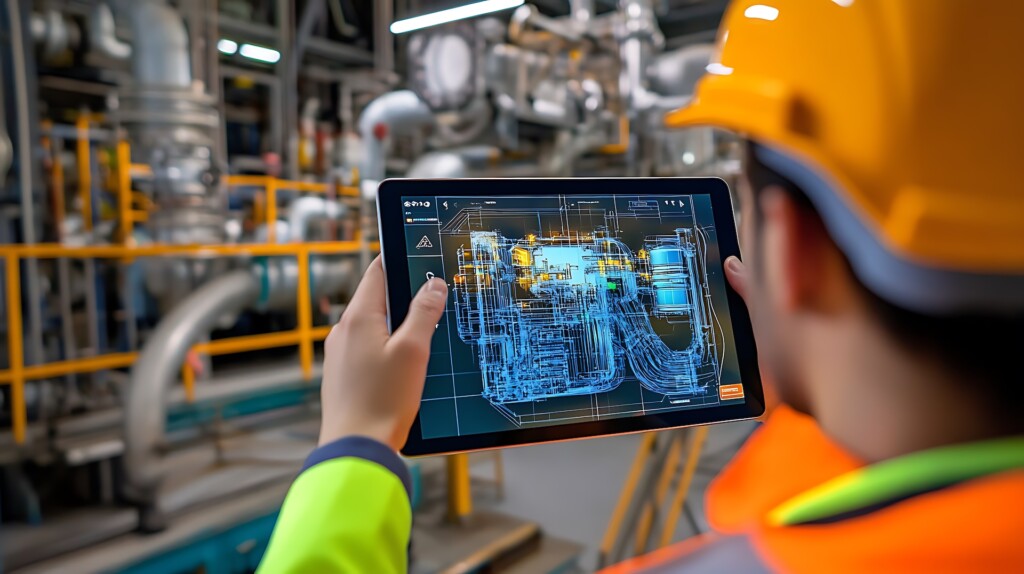
Common data environment (CDE) key to success
When working with digital as-built information, a common data environment (CDE) is key to building a single source of truth. A CDE enables all parties — the owner, designers, contractors, surveyors and others — to access one federated model for all project information.
According to the international standard ISO 19650, a CDE is an “agreed source of information for any given project or asset, for collecting, managing and disseminating each information container through a managed process.” CDEs often use unique, standard identifiers to track all project information. Data can be categorized and assigned a specific suitability status to guide anyone accessing the data regarding its reliability, accuracy, and intended use. A revision control system can make only specific revisions available for use by the project team, to make sure everyone is working from the correct information. Security measures are typically employed to maintain data integrity and controlled access to project information.
An effective CDE is typically geared around a specific collaboration platform and cloud-based data storage. Design collaboration platforms have advanced significantly in recent years and enable information to be tracked and tied to specific project elements, with the system automatically notifying and delivering information to people as needed. Rather than waiting for hardcopy as-builts that show field changes, team members can be informed of changes in near real-time, helping keep future work on track.
Cloud-based data storage enables project team members to access current data regardless of workers’ physical location. Shared network drives have also been used for collaboration but are often limiting in speed and accessibility. As-built documentation on the cloud provides a central, accessible location for data.
Regardless of methodology, as-built documentation forms a vital part of project information. It provides accurate records that aid owners, designers, contractors, governmental agencies and other parties. In the future, it may even guide AI tools that learn lessons from previous projects and apply those lessons to future designs.