It’s not quite at Tony Stark-level interactivity, but it’s getting close.
Virtual Reality (VR) is becoming a valuable tool in digital prototyping, enabling manufacturing and design engineers to create, test, and refine products in immersive, interactive environments.
By integrating VR with CAD (Computer-Aided Design) software, PLM (Product Lifecycle Management) systems, and real-time physics simulations, engineers can gain unparalleled insights into product behavior before physical prototyping. But there are several technical intricacies of VR in relation to digital prototyping and its applications, integration challenges, and benefits to manufacturing.
Integration of VR with CAD and PLM
Modern VR-based digital prototyping heavily relies on CAD and PLM integration. CAD software exports 3D models in VR-compatible formats (such as FBX, OBJ, GLTF) that allow engineers to examine prototypes within the virtual environment. When paired with PLM systems, engineers can track version histories, collaborate in real-time, and integrate design modifications directly into the production workflow. This connectivity ensures that design iterations remain structured and accessible to all stakeholders.
To enhance VR compatibility, many CAD software solutions incorporate native VR apps or VR plug-ins, which allow direct visualization of engineering-grade 3D models in VR without cumbersome file conversions. These tools support parametric modeling and real-time geometric modifications, ensuring high fidelity in virtual environments.
Real-time physics-based simulations
VR goes beyond static visualization by enabling real-time physics-based simulations that engineers use to assess product performance under various conditions.
Simulations can include:
Structural Analysis: Finite Element Analysis (FEA) simulations are rendered in VR, allowing engineers to visually inspect stress distributions and failure points in a virtual space.
Fluid Dynamics: VR-integrated Computational Fluid Dynamics (CFD) simulations enable engineers to observe airflow patterns, heat dissipation, and liquid flow behaviors from a first-person perspective.
Material Deformation: Soft-body physics can replicate material flexing, bending, and breaking under applied forces, giving engineers an intuitive understanding of how materials respond to different loads.
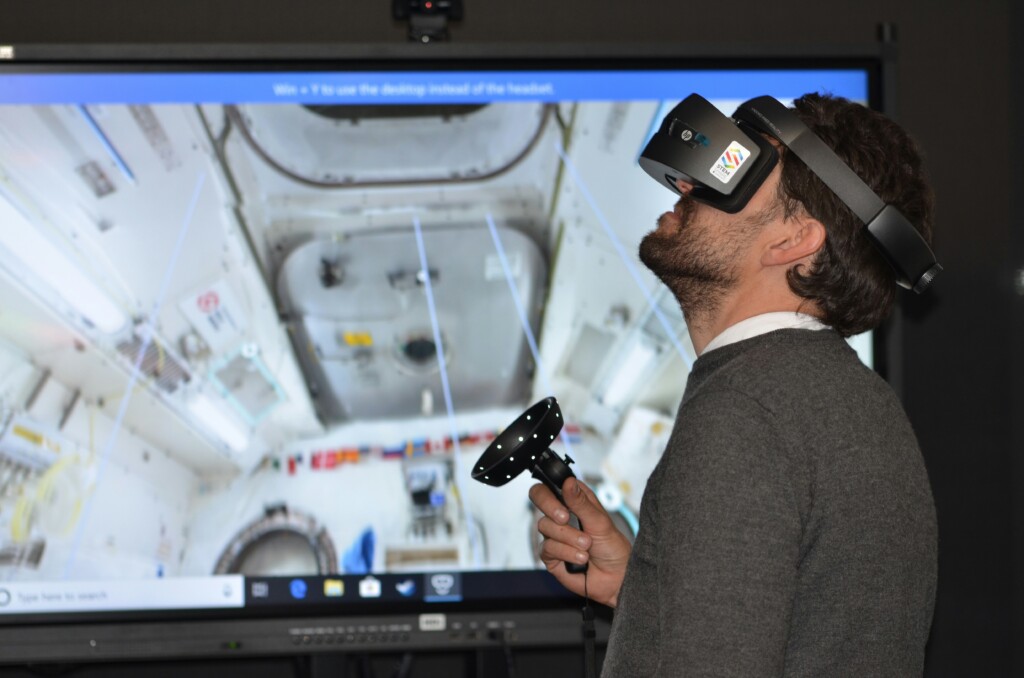
Haptic feedback and realistic interaction
One limitation of traditional digital prototyping is the inability to physically interact with the model. VR overcomes this challenge by incorporating haptic feedback devices, which simulate tactile sensations and resistance. Such devices allow engineers to “feel” surfaces, textures, and resistances as they manipulate virtual components.
In addition to haptics, real-time rendering techniques such as ray tracing and shadow mapping improve visual realism in VR environments. High-performance GPUs enable photorealistic rendering, ensuring that materials, lighting conditions, and reflections closely mimic real-world properties. By integrating physics engines developed by a number of different companies, VR prototypes can react dynamically to user interactions, providing a near-physical testing experience before production.
Design validation and ergonomics testing
Manufacturing engineers can use VR for comprehensive design validation before committing to expensive tooling and fabrication. Dimensional accuracy checks assess tolerances and fitment by placing components in a simulated assembly line, while ergonomics assessment using VR simulations allow engineers to test human-machine interactions, ensuring that equipment is comfortable and efficient for operators.
Instead of relying on physical mock-ups, engineers can conduct virtual usability studies, allowing stakeholders to evaluate user experience and product functionality in various conditions.
Industry-specific applications of VR prototyping
Automotive: Car manufacturers use VR to perform full-scale vehicle prototyping, enabling designers to test aerodynamics, visibility, and cockpit ergonomics before building physical models.
Aerospace: Engineers visualize and test complex aircraft components, such as turbine blades and fuselage assemblies, in VR environments with real-world physics simulations.
Consumer electronics: Companies test user interfaces and device form factors in VR to refine designs based on virtual consumer feedback.
Medical device manufacturing: VR enables precise simulation of surgical instruments and implants, helping engineers refine designs for biomechanical compatibility.
Technical challenges and solutions in VR prototyping
Despite its advantages, VR prototyping presents several technical challenges. Combining multiple engineering datasets (FEA, CFD, PLM) into a cohesive VR simulation can be challenging, but standardized file formats (USD, STEP, and FBX) streamline data exchange across platforms.
Running detailed CAD models in VR can be costly, as the high computation output requires powerful GPUs and optimized software workflows. Using Level of Detail (LOD) algorithms and real-time model decimation can improve performance without sacrificing accuracy. These algorithms optimize performance by adjusting the complexity of 3D models based on their distance from the viewer or their importance in the scene. Here’s how they work:
Dynamic mesh simplification – LOD algorithms swap high-detail models for lower-poly versions when objects are further away, reducing GPU load without affecting perceived visual quality.
Adaptive rendering – By prioritizing detail only where needed (on user-interacted components), LOD ensures real-time rendering efficiency.
Improved frame rates – LOD prevents frame rate drops by decreasing the polygon count in non-critical areas, ensuring smooth VR interactions at 90+ FPS (critical for reducing motion sickness).
Memory optimization – Less-detailed models free up GPU memory, allowing for larger assemblies and complex simulations without performance bottlenecks.
Hybrid use with culling techniques – Combined with occlusion culling (hiding objects not in view), LOD further enhances computational efficiency.
Future trends
The future of VR-based digital prototyping in manufacturing is set to become even more powerful with advancements in AI-driven automation, cloud-based collaboration, and hybrid AR-VR environments.
AI-driven automation integrates machine learning algorithms that analyze designs in real time to detect structural weaknesses, suggest material optimizations, and even predict potential manufacturing defects before physical prototyping begins. By continuously learning from past designs and simulations, AI can help engineers refine product performance and reduce costly trial-and-error iterations. This capability will significantly shorten development cycles while improving the reliability and manufacturability of new products.
In addition, cloud-based VR collaboration will redefine how global engineering teams interact with digital prototypes. Instead of requiring high-end local hardware, cloud-rendered virtual workspaces will allow engineers to access and manipulate detailed VR models from anywhere in the world. This technology will enable real-time design reviews, remote troubleshooting, and seamless integration with PLM (Product Lifecycle Management) systems, ensuring that teams remain aligned even when working across different locations. Cloud-based VR will also facilitate large-scale manufacturing projects by enabling multiple stakeholders—from designers to production managers—to interact with virtual prototypes without needing specialized workstations.
Furthermore, the rise of AR-VR hybrid environments will bridge the gap between digital and physical prototyping. By overlaying VR-generated 3D models onto real-world objects using Augmented Reality (AR), engineers will be able to test virtual components in real-world settings without requiring a full digital or physical setup. This will be particularly useful for ergonomics testing, assembly validation, and factory layout optimization, where seeing how a virtual component interacts with real machinery or workspace constraints is crucial.
As these technologies continue to evolve, VR-based digital prototyping will become an intelligent, collaborative, and highly integrated system, streamlining manufacturing workflows and enabling faster, smarter product development.