Siemens has sponsored this post.
Engineers love to understand how stuff is made; this is where companies like SKARTEK shine. Its cofounder and executive manager, Christophe Payon, explains that the company specializes in designing, installing and maintaining industrial processes.
“Our customers are international manufacturers,” he says. “Our job is to produce their manufacturing lines. We do it all by ourselves, the programming, electrical and mechanical.”
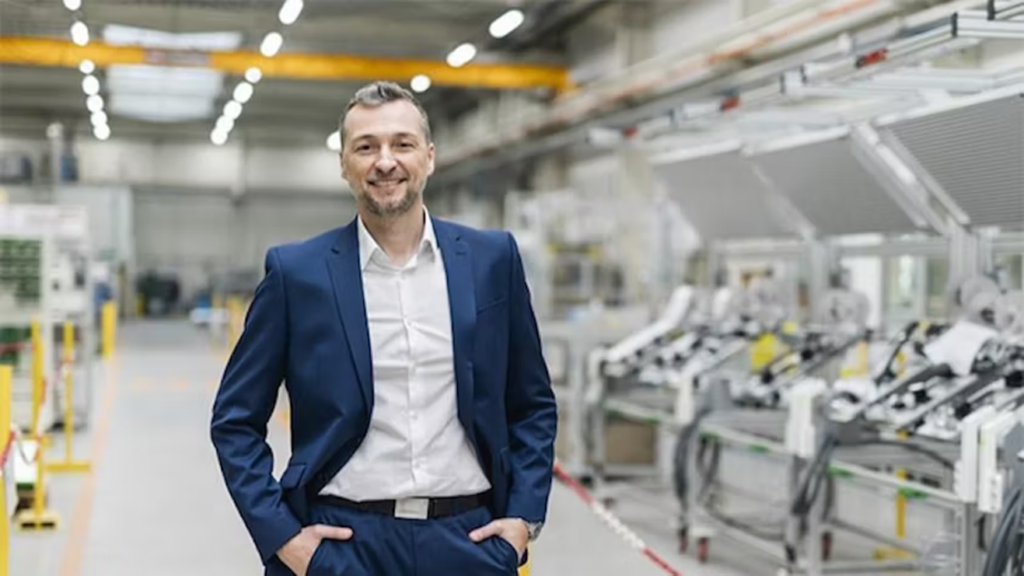
For each project, SKARTEK’s goal is to hand off an end-to-end, automated, manufacturing solution to its automotive, aerospace, railway, construction and electronics customers. To achieve this, the company employs engineers of various specialties, on-site manufacturing equipment and a manufacturing research lab. SKARTEK also works with SOVA Digital and its partner Siemens Digital Industries Software to audit, optimize and enable its digital transformation. SOVA Digital helps manufacturers integrate digitalization, optimization and Industry 4.0 solutions into their current workflows.
To learn the critical role Siemens and its software played in SKARTEK’s digital transformation, read more.
How and why SKARTEK needed a digital transformation
As SKARTEK grew, its software and processes became ill-equipped to manage its complex projects and their many stakeholders. “We started with two people; right now, we are more than 55,” says Payon. “We needed to implement a totally different way of working, as we were not able to manage our classical projects the same way. We were looking for a new support software to help us improve our organization.”
The company selected Siemens Teamcenter and Solid Edge to update, digitize and digitalize its workflows, data and development processes. This digital transformation, aided by SOVA Digital, produced benefits that were significant — some even unexpected — for Payon and his team.
The obvious, and not so obvious, design benefits of digital transformations
Payon notes that no production facility is the same. As a result, SKARTEK must adapt its solutions and workflows to the current customer they support. Nonetheless, the company has found that it can reuse many of the parts, concepts and designs created throughout its history and adapt them to different facilities.
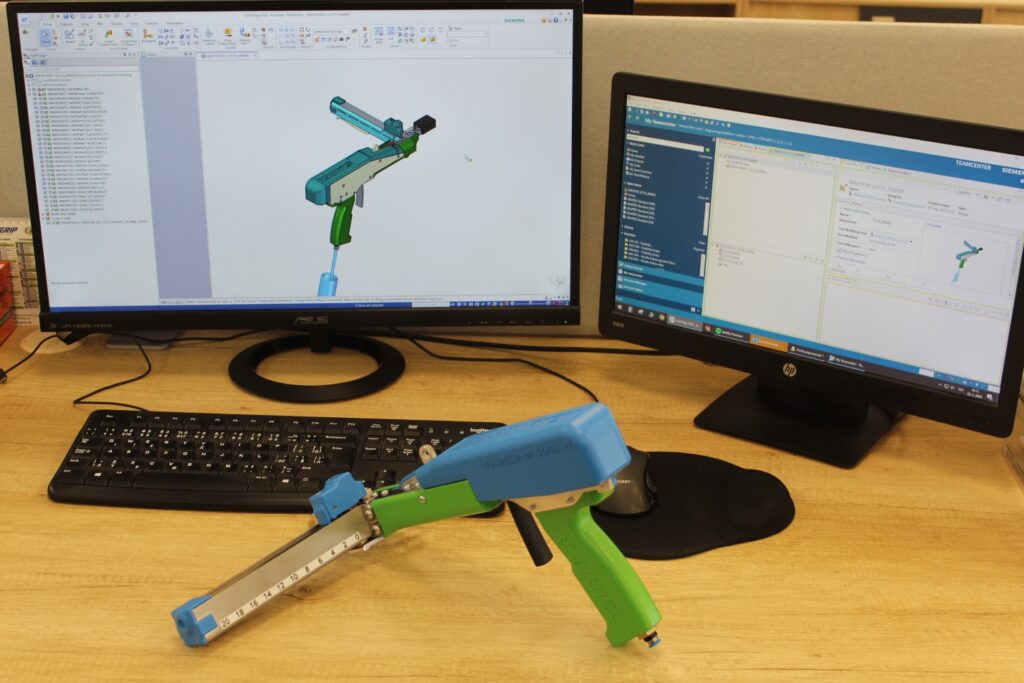
“When doing a project, we want to reuse what is done and design something new, if needed,” Payon clarifies. “We are selling optimization. So, we want to sell the optimization we use in our own system: Design it once and reuse it in future projects. In the past, this wasn’t possible. But with Teamcenter and Solid Edge we can design once and adapt it for another project. It really decreased the time, cost and makes us more competitive for the customer.”
The company also discovered some obvious and unforeseen ways reusing parts can speed up the development of new manufacturing systems. The obvious benefit is when a design from one project can be used, one-to-one, with another system. Now instead of re-inventing-the-wheel, SKARTEK just inserts the part it has already designed, evaluated and approved for a specific application. If the application is slightly different than the original project, then some aspects of the part may need a redesign. But since SKARTEK already has a good starting point, the engineers need only to reoptimize the part for its new application — saving development time and money.
As for unforeseen benefits, Payon points to the members of his team that need a finished design to start developing a downstream task, part, workflow or automation. Consider an engineer programming the movements of a robotic arm. While other members of the SKARTEK team develop a new gripper for the arm, the engineer can use an old gripper design to get started. This enables the engineer and gripper designers to work in parallel.
Yes, the gripper the engineer is using will be different. And yes, those differences may force the engineer to adjust down the road. But with the previous gripper design, the engineer can get 80 percent of the way there before receiving the new design. They can then swap out the grippers, once the new one is available, to complete the remaining 20 percent of their work.
“Our target is to be a more flexible company compared to our competitors,” says Payon. “We need to be more flexible, and this flexibility is increased by collaboration. By using the software like Solid Edge and Teamcenter from Siemens, which allows us to be competitive.”
The role of data management and simulation in production line design
In the past, SKARTEK would often lose data to unstable software applications. If the program failed at an inopportune time, hours of design work could be lost. And since data was not effectively managed, even if a design were properly saved, it could be lost, forgotten or invisible to members of the team that forgot, or were unaware, of its existence.
With a digital transformation and proper data management tools, like those found in Teamcenter, engineers can access the data, information and IP they need when they need it. It is also much easier to search through the history of a company’s data lake to find solutions, or a good starting point, for a given challenge.
This easy accessibility to information, data and designs also simplifies simulation workflows. “For easy projects,” says Payon, “simulation isn’t done. We are using simulation for [developing] bigger lines and when we need a lot of new designs for the work. Simulation is important as it gives the feedback on our technical solutions.”
Payon estimates that about 10 to 25 percent of SKARTEK’s projects require simulation. But since the projects requiring simulation are complex, and CAE has traditionally been a long, hard and tedious process, these projects represented a significant amount of work. Thus, the workflow boosts Solid Edge and Teamcenter bring to SKARTEK’s simulation experts are a significant boon.
“We design everything from Solid Edge and can send it to all the other software applications that it communicates with,” says Payon. This streamlined the simulation workflow as 3D models were readily available and compatible with the CAE tools of choice. In fact, many of the simulations SKARTEK requires can be done within Solid Edge. Giving the company’s designers a familiar user interface and workflow to better assess the performance of their designs.
Digital transformation isn’t easy; it’s necessary.
Implementing Solid Edge and Teamcenter was not easy. But Payon and his team notes that it was more than worth the effort.
“It was difficult to implement, we knew it would be a challenge and take time, but right now, it’s about the advantages,” says Payon. “It’s challenging to convince the guys that it’s a good idea as they don’t always see the benefits. After three years, [stakeholders] say we know why we are here. It’s not easy to adapt but it was the right decision to make.”
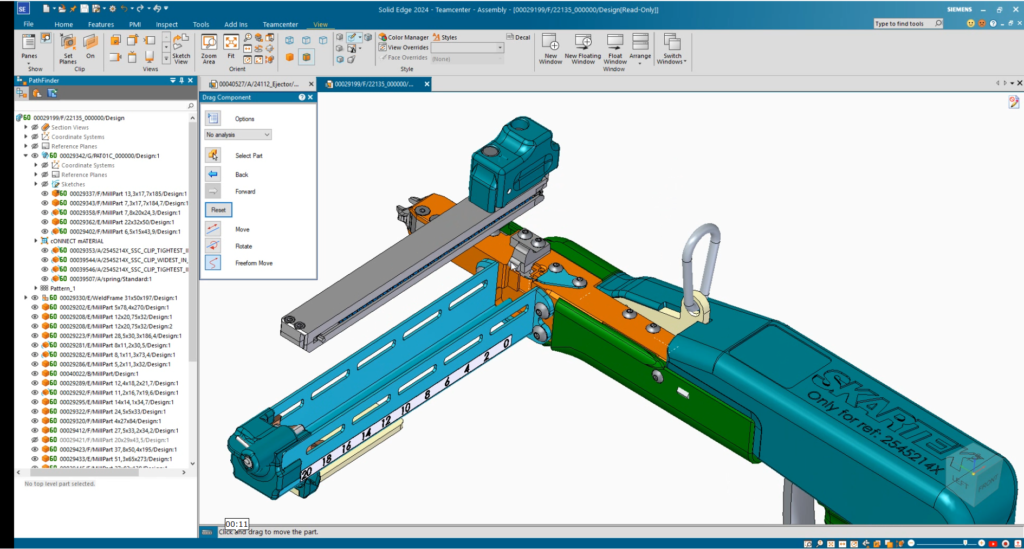
In fact, SKARTEK crunched some numbers to backup these claims. By adding Solid Edge to the company’s workflows, project time was reduced by 10 to 15 percent. This alone would be impressive, but its success was surpassed by the addition of Teamcenter — which enabled the company to reduce project time by 30 percent.
The main sources of these productivity gains came from three aspects:
- Teamcenter’s ability to create a single design environment which enabled teams to work concurrently on the latest, up-to-date, engineering information.
- Teamcenter’s collaboration and data visibility features enabling everyone to remain on the same page, work together and avoid rework.
- Solid Edge’s ability to dynamically manage and update CAD models to reduce the chances of any errors during product development.
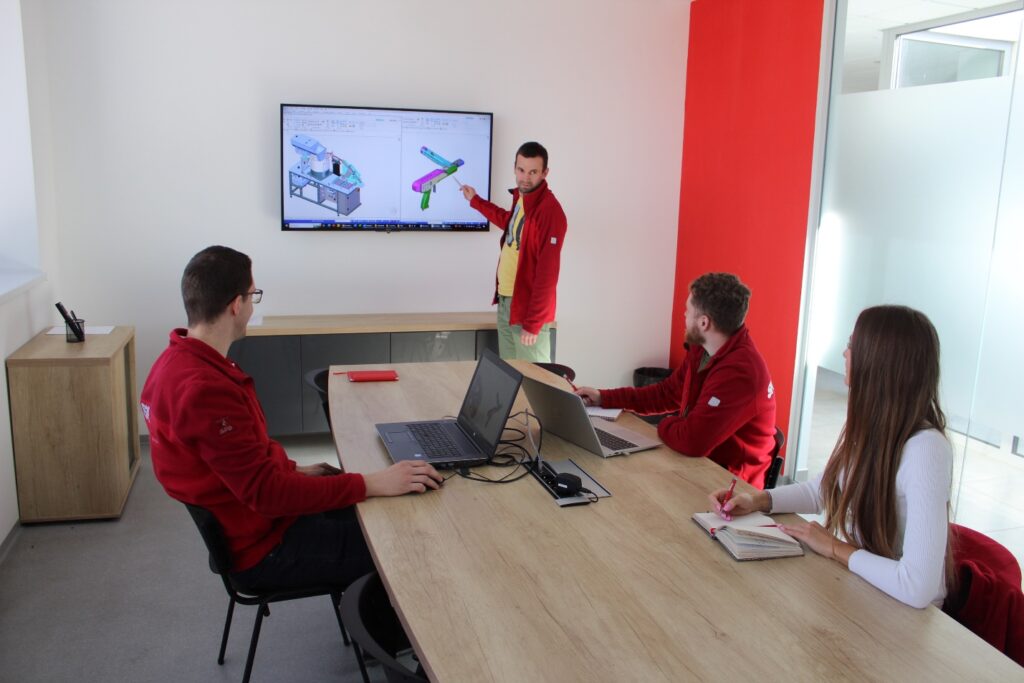
With such a focus on Teamcenter’s ability to maintain and manage data, its no wonder that when first introduced to the software, Payon’s team “were thinking in the beginning that it was a standards solution. But no, it’s a design data management solution you can adapt to your processes. Not many in this market can adapt to your way of working.”
He adds, “When Siemens first proposed Teamcenter, we thought it was nice, but for bigger companies. We thought it would be harder to utilize in smaller companies. In the end, with the tuning of Teamcenter to our needs, we found a way to use it that is dedicated for us. We added Teamcenter and adapt it for our needs.” And in so doing, SKARTEK is reaping many rewards.
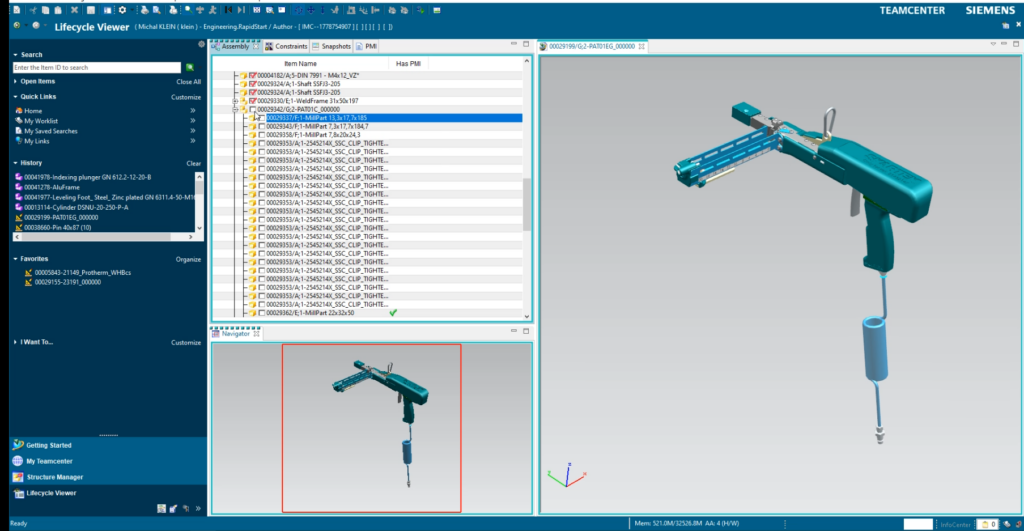
If you, like SKARTEK, want to benefit from better performance, improved re-use of CAD data and a more integrated product development process, learn more about Solid Edge and why you should switch now.