Aerospace companies including ULA and ArianeGroup are using engineering software to tackle the unique challenges of rocket design.
From design to software testing, digital twin technologies and computer simulations are helping rocket makers get to the launch pad faster.
On October 4, Vulcan Centaur, the brand new heavy-lift rocket developed by United Launch Alliance (ULA), lifted off from its launch pad at Cape Canaveral Space Force Station in Florida for its second test flight.
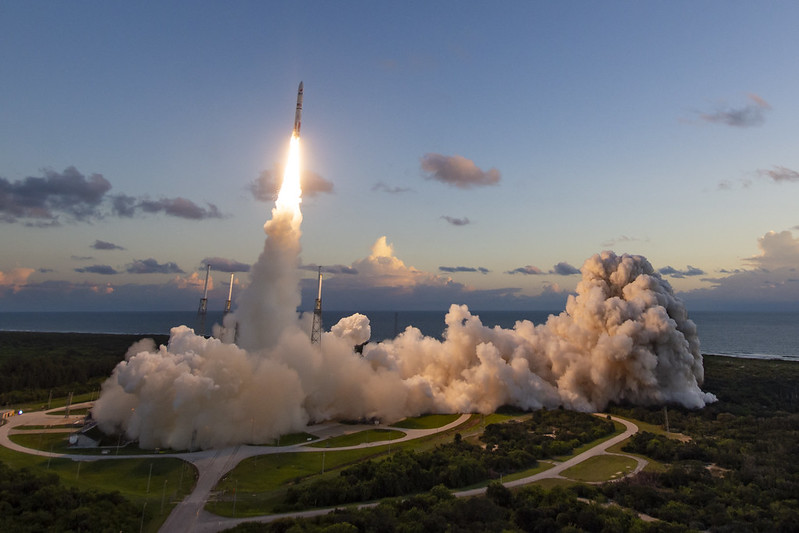
The mission, carrying a mock payload, was key for ULA to obtain certification to commence commercial operations and begin flying sensitive U.S. military satellites. The launch took place eight months after Vulcan Centaur’s debut (which put into orbit the failed Peregrine lunar lander in early January), and went nearly without a hitch (about half a minute after lift-off, one of the rocket’s strap-on boosters spat out several bursts of scorching fragments, but the incident, later attributed to a nozzle failure, was described only as a minor glitch).
In a post-flight conference, ULA’s CEO Tory Bruno said that the firm expects to fly Vulcan Centaur ten times next year. Such a speedy scale-up to full operations would be impossible in the past, ULA’s chief rocket scientist John G. Reed, told Engineering.com. The Colorado-headquartered rocket builder has made it happen thanks to the extensive use of new digital twin technologies in their design and manufacturing chain.
“Normally, it takes two to three years for rockets to get up to rate,” Reed said. “But we want to get up to full rate by the end of next year, launching twice a month. We can do that because the digital elements in the ecosystem give us the confidence we need to go that fast.”
Digital twin test bed
Vulcan Centaur, conceived in 2014, is not as groundbreakingly innovative as SpaceX’s reusable Falcon 9, but it still features a range of novel technologies. Its Centaur V upper stage, the fifth iteration of a system in use since the 1960s, can be re-ignited three times to reach three different orbits — a useful feature for deployments of mega-constellations such as Amazon Kuiper, to which ULA has sold 38 Vulcan Centaur launches.
The Vulcan first stage combusts an environmentally friendly propellant combination of methane and liquid oxygen, which produces fewer pollutants than the refined kerosine consumed by SpaceX’s Falcon 9. Although not capable of autonomous landings, the Vulcan Centaur first stage is made of modular components that can be recovered and refurbished for repeated use.
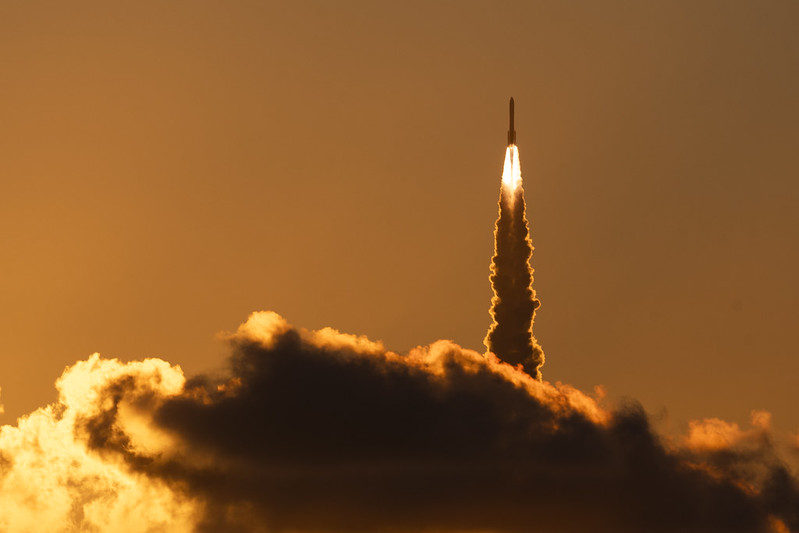
The rocket was a digital twin testbed for ULA, said Reed, but finding the right place for the technology in the development process wasn’t straightforward.
“We’ve been working on this for more than a decade,” said Reed. “When we first started, it wasn’t clear how to get value out of the digital twin. A lot of the focus was on being able to do faster iterative development, to tweak and try things, and to design more quickly. But that wasn’t where the value was for the organization that was doing it.”
Rockets are a specific kind of technology. Even with dozens of launches per year, their stages and boosters roll off production lines in very small numbers. Unlike most machinery used by humankind, a rocket has a very short lifespan — barely a few days pass between its roll-out onto a launch pad and the moment this shiny new thing turns into a useless piece of debris. Once the rocket is in the air, there is nothing technicians on Earth can do if any of its components start to malfunction. Rocket systems are also super complex and super dangerous, requiring extensive testing before each flight.
Too vast to crunch
Rocket makers have been using digital simulation techniques in design and prototyping ever since the first commercial CAD suites were introduced in the 1970s. For ULA, a joint venture between Lockheed Martin and Boeing, it turned out quite impossible to simply integrate those decades-worth of legacy systems and technologies into a single digital twin simulation.
“The digital twin technologies that are currently available are still very expensive and hard to go ingest those kinds of existent materials,” said Reed. “Rather than saying — ‘I want to have a twin of the entire end-to-end system’ — we wanted to figure out, how do we get the practical benefits out of twins, and how do we fold them into the evolution of our systems.”
The ULA team “hybridized” the Vulcan Centaur “down to the component level,” creating digital twins of individual elements and subsystems while at the same time ensuring that none of these partial twins gets computationally out of hand.
“It’s less complex than the high-fidelity simulation work that we do to create rocket trajectory design and calculate loads,” Reed said. “Our digital twins require probably an order of magnitude less compute power, so we’ve been able to do it within the compute capability that we have within the enterprise.”
A digital replica of the flight computer allowed the team to put the flight software through its paces and simulate situations it might encounter as the rocket goes through the pre-launch and launch sequence and flight. Similar models of the rocket’s avionics enabled engineers to gain understanding of the rocket’s motions as it clears the launch tower. Some of these insights, said Reed, would not be possible to obtain through traditional hardware testing methods.
No hardware in the loop
Streamlining the testing process is one of the main benefits achieved through digital twin technologies, said Reed. Software can be tested before hardware gets built and delivered. Results of these tests feed back into the hardware development. Only once engineers gain confidence that the solution works do they move toward hardware-in-the-loop (HWIL) testing.
“One of the measures of the value of ULA’s digital engineering program is measured by hours saved in the HWIL environment,” Reed said. “Our digital environments save us time in the development, software integration and early testing. The digital engineering environments also become enablers to strategic objectives and new missions.”
Teams can run parallel simulations in ULA’s virtual System Integration Lab (SIL), which has taken some of the workload off the traditional HWIL integration laboratory.
Using the physical testbed, involving the entire launch site and rocket systems, comes with a high price tag. The virtual SIL enabled ULA to pre-test systems virtually at a fraction of the cost.
“We now have digital twins of that test environment that allow the engineers to go refine the procedures and go test flight operations in a lab environment, but virtually,” said Reed. “Instead of paying for additional engineering development units and all of those kind of costs.”
ULA’s European counterpart ArianeGroup has also been using digital twin technology to design, build and finetune its new-generation Ariane 6 rocket, which, like Vulcan Centaur, nailed a nearly flawless debut flight this year.
ArianeGroup’s Chief Technical Officer Hervé Gilibert told Engineering.com that digital twins of the entire rocket and its subsystems play a crucial role in pre-launch testing.
“We can explore the functional behavior and the performance of our rockets in flight in all possible degraded situations, thus allowing us to check the robustness of the design” Gilibert said. “For the development of launchers, there is no other way of working, except if one accepts to take the risk to fail several times in a row during the first several flights. This would be another approach, much more risky business wise.”
As rockets for subsequent flights are usually already produced at the time of the debut flight, correcting faulty designs after an in-flight failure occurs would further increase the cost, Gilibert added.
A collaborative environment
Another major advantage in using digital twin systems comes from allowing the designers, engineers and the manufacturing teams to access the same digital environment, said Reed, essentially digitally connecting the design center with the factory.
“You end up creating a twin of the processes and tools that can integrate the analysis work that the engineering community is doing and create a digital 3D model of the system and elements that are going to be fabricated at the factory,” said Reed. “It allows you to create a bill of materials that is shared effectively between an engineering bill of materials and a manufacturing bill of materials, where some of those components are built, some of them are bought, and so you end up with a shared source of truth.”
As “most out of the box solutions don’t fully capture the complexity of rocket systems,” according to Reed, ULA relies on a range of model-based systems engineering tools combining commercially available and custom-made solutions (the company wouldn’t disclose which software they use for security reasons).
Reed expects the technology will fully come into its own when ULA begins exploring engine reusability and increasing the launch cadence. “We’re going to be constantly looking at where twin development provides a cost benefit,” Reed said. “Once we start looking at engine recovery and reuse, there will be a lot of evolving twin developments as the product comes to the market, but also as the market and customer needs evolve and emerge.”