Branch Technology CEO Ryan Lusk discusses the state of 3D printing in construction.
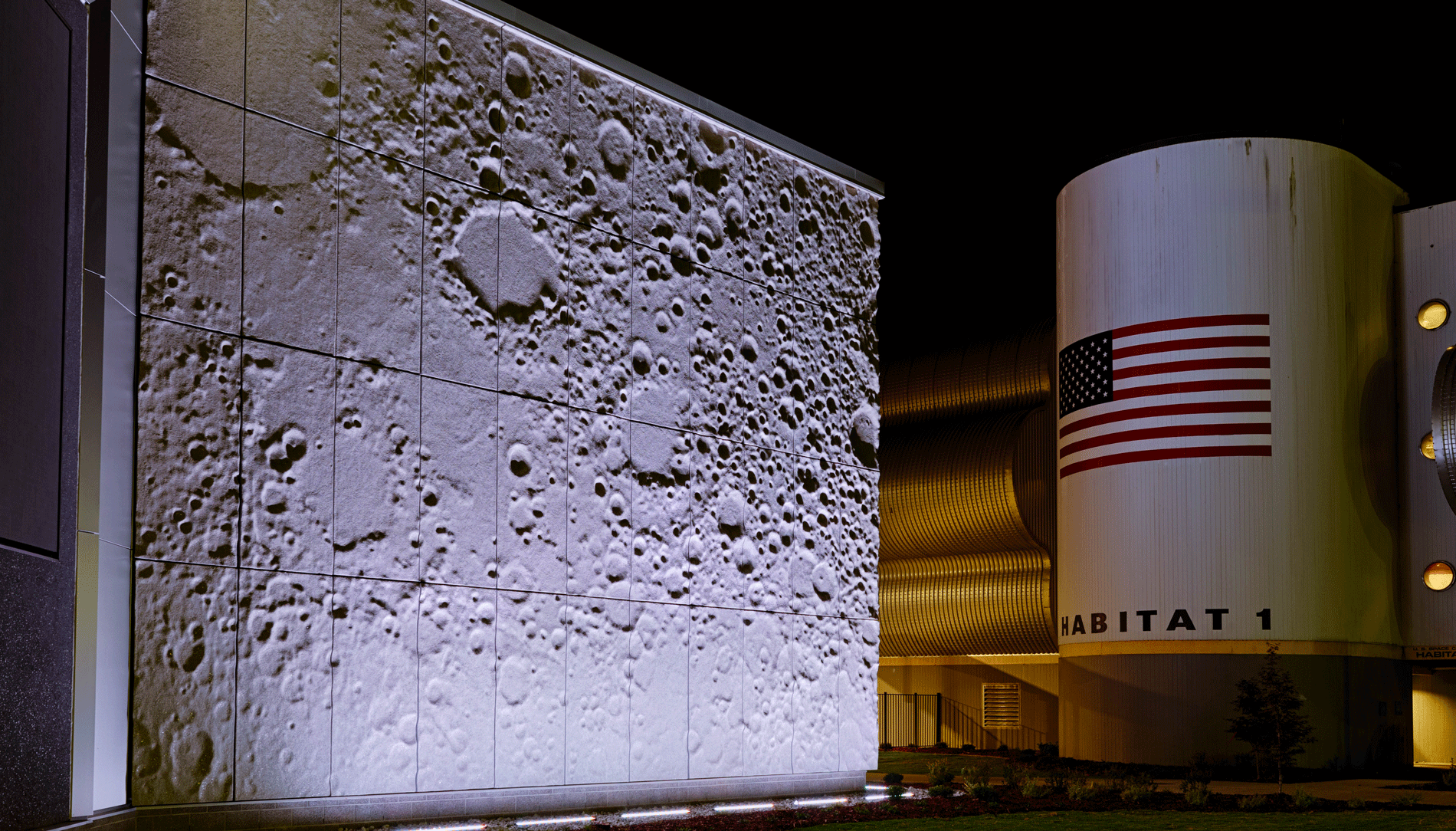
“If it ain’t broke, don’t fix it,” should hang above the door of every self-respecting engineering school. Unfortunately, for many technology companies these days, preferences tend toward the updated version: “If it ain’t broke, it doesn’t have enough features yet.”
Of course, assessing whether a product or process ain’t broke is no simple matter. The pace of cultural, environmental and technological change in the 21st century is such that products and processes can become broke simply by remaining static.
Take construction, for example. It’s a sector well-known for hewing to the old “If it ain’t broke…” adage and yet, as demand for additional housing and revitalized infrastructure continues to increase, the pressure to find new, more efficient methods is increasing as well.
What will it take to shake construction out of the doldrums?
How did it get there in the first place?
I sat down with Ryan Lusk, CEO of Branch Technology, to talk about where the construction sector is heading and how 3D printing fits into that future.
Engineering.com: Why do you think we haven’t seen as much technological disruption in construction compared to other sectors? Is it a matter of having to overcome regulatory hurdles, or does it just come down to inertia?
Lusk: That’s certainly the million-dollar question. From a data standpoint, there’s a McKinsey study from a few years ago that ranked industries by their adoption of new technologies and innovation. Construction was second to last – only above fish hatcheries.
Why is that? Broadly, there is an inertia component, but construction is also really a collection of sub-industries, each with competing interests and incentives. You have the design side, with architects who use cutting-edge software, from early CAD and CAM to today’s AI-driven generative design tools. That technology has dramatically outpaced manufacturing capabilities and cost-effectiveness, which has been a limiting factor.
Then there’s development, which includes cost structures and financing, and finally, the actual construction – the general contractors and installation teams. These groups often have competing incentives. Architects typically aren’t too aggressive about adopting new technology. We jokingly say they want silver medals – they don’t want to be the guinea pigs.
Developers tend to be more open to technology, and in the built-world side, general contractors are already struggling with a lack of skilled labor. They’re focused on what they already know how to do, so adopting anything new is a challenge.
If you ranked these stakeholders by their priorities – design, cost, installation – you’d get very different rankings, which creates a difficult environment for disruption. Everyone is profitable enough that they don’t feel the need to innovate or adopt new technology.
But 50 or 100 years into the future, people might find it crazy that we used to drop all these materials out in the woods or an open field, and then an army of workers would assemble a structure on-site. We wouldn’t do that for any other product we buy.
How does what you’re doing at Branch Technologies apply here?
We 3D print a lattice structure called the Branch Matrix, which is similar to cell walls in our bodies and provides the overall form, function, and design. We then infill it with construction-grade foam and robotically mill it down to its final geometry.
The result is an incredibly lightweight yet strong composite product, fine-tuned for various construction applications.
This process falls under the umbrella of additive manufacturing. However, while most additive manufacturing approaches focus on how much material needs to be layered up – such as FDM printing or concrete printing for residential housing – we ask, “How little material can we use while still achieving the required performance and structural characteristics?”
In fiscal year 2024, we experienced 300% growth, primarily driven by our facade product for exterior building cladding. We also have several other applications in development.
Facades are primarily used in new construction. However, we have also developed a patented energy-efficient retrofit product called Branch Regenerate, which is currently being installed at Kirtland Air Force Base in Albuquerque, NM.
This product follows a similar material stack but involves additional steps. We start with a high-definition LiDAR scan of the existing building, typically a 50- or 60-year-old structure with bowed or cracked walls and architectural features. Using this scan, we create a 3D model that drives our production processes. We then mill the backside of our facade panels to accommodate architectural features before installing them to enhance the building’s energy efficiency.
Do you see the retrofit approach you’re taking in Albuquerque and elsewhere as a way to overcome some of the hurdles to innovation we’ve been discussing?
Yes, exactly. In this case, we actually have something of a regulatory tailwind. Energy efficiency mandates are looming for 2025 and 2030, and sustainability is top of mind for many. Beyond that, there’s a real cost driver—some studies estimate that 40% of energy usage is lost through a building’s facade and envelope. That makes energy efficiency upgrades a priority from both a regulatory and a cost perspective.
Right now, there aren’t many good or cost-effective options. Tearing down and rebuilding a structure isn’t realistic—it’s disruptive, costly, and requires permitting and approvals all over again. Removing and replacing an existing facade is also highly disruptive, often requiring tenants to vacate the building. So, developing a rapid, cost-effective recladding system makes a lot of sense. By producing components asynchronously while other trades are working on their parts, we save tremendous time and labor on the job site.
On the topic of labor, it’s well known that construction is facing a labor shortage. Does your technology address that challenge, or is it more orthogonal to it?
It depends on the project, but labor is a big factor. To drive adoption in the construction industry, you need the “Holy Grail” of cost parity or even savings. We often compete with precast GFRC [Glass Fiber Reinforced Concrete] panels and other heavy, bulky products.
So, we conducted a case study on a 50-story tower that we hope to work on. Originally, the facade was designed for precast GFRC or architectural precast. Using our facade panels instead would save over 34 million pounds in weight compared to those alternatives. That reduction allows the slab edge on all 50 floors to be reduced from 15 inches to about 6 inches.
From a labor standpoint, traditional precast requires dedicated crane time and skilled workers to hoist and weld heavy panels. In contrast, our panels can be installed using a simple swing lift or cherry picker.
Where do you see construction heading over the next 10 years? And how do you see 3D printing, or Branch specifically, playing into that?
I think the adoption curve of new technology is accelerating. I just attended the CREtech conference in New York. It was really exciting and encouraging to see the momentum for all things proptech and contech: smart homes, smart buildings, data management and energy management technologies.
In construction, there’s a distinction between residential and commercial applications. Different technologies will gain traction in each. In residential, companies like Icon are doing intriguing work with 3D printing. In commercial, the approach will have a bigger impact as we refine our products to influence more of the total building budget and project scope.
One application we’re excited about is temporary homeless shelters. Our technology allows us to create lightweight, rapidly assembled shelters that can be set up in an hour or two. They are secure, have lockable doors, self-leveling feet and HVAC, providing a dignified housing solution. The leasing model makes these shelters a cost-effective solution for cities, municipalities and charitable organizations. After use, they can be sanitized and relocated to areas in need, whether for homeless encampments, natural disaster relief, or refugee housing.
Another particularly fun and meaningful project we did was for NASA’s new Space Camp Operations Center, where they bring in the next generation of STEM students who will hopefully become tomorrow’s astronauts and engineers. After we did some ideating with them on what the building should look like, including the façade and a large entryway, we were able to obtain a LIDAR scan of the actual surface of the Moon. Using that data, we recreated the surface of the Moon on both sides of the building.
It’s a really beautiful recreation of the actual lunar surface, but it also serves as a symbol. In the early days, we were focused on extraterrestrial applications while we were developing this technology. Now, we’re bringing it back to Earth to solve problems here.