Improving binder jetting and WAAM processes, more Nano Dimension drama, and aluminum forming with PLA+ dies.
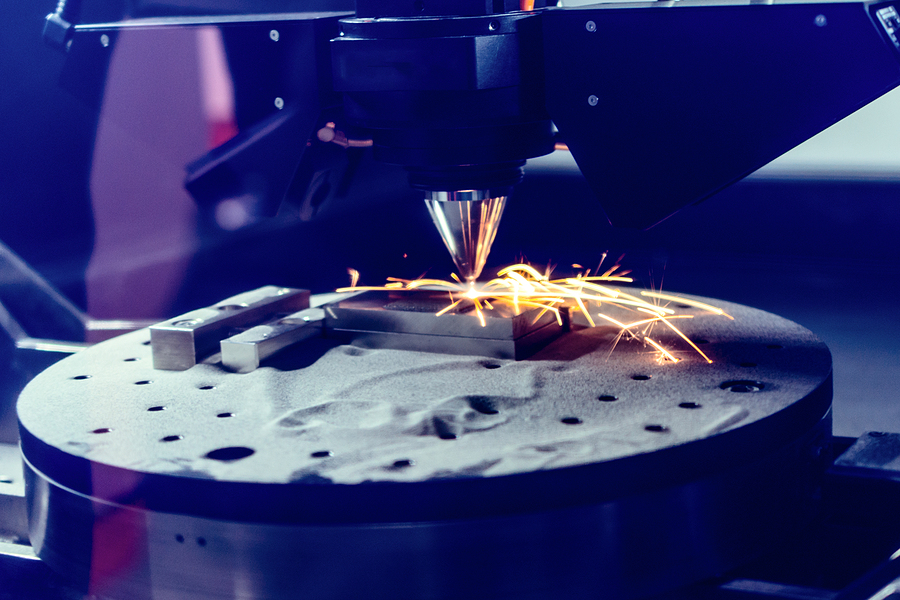
Welcome to the first edition of the engineering.com Additive Manufacturing Progress Update, a monthly column focusing on the latest in 3D printing research and business – with a little fun thrown in at the end.
Let’s get to it!
Additive manufacturing research review
In this section, we review recent additive manufacturing research papers published in open-access formats, summarizing each article with comments from the researcher(s) when possible. We also include links to the full texts for further reading.
Improving rapid sand casting with additive manufacturing
A team of engineers from the University of Johannesburg, Cape Peninsula University of Technology, Tshwane University of Technology and the Air Force Institute of Technology, Nigeria took an in-depth look at the effects of various sand properties on the quality of rapid sand molds and cores created with additive manufacturing.
Two of the most significant properties they identified were grain shape and packing density, both of which impact conductivity and heat capacity during the casting process. The researchers suggest that closer attention to sand properties as well as hybrid sands incorporating engineered additives could improve the thermal and mechanical properties of cast parts.
Spatial variation of green density in binder jet additive manufacturing
Binder jetting processes (BJT) and L-PBF processes are both known for having issues with geometric distortions due to shrinkage. However, while L-PBF can correct for this in-situ by spreading more powder than a part’s layer thickness, BJT keeps the powder layer constant, resulting in greater distortions. Two engineers – Albert To at the University of Pittsburgh and Basil Paudel at National Taiwan University – tackled this problem by studying the effects of geometric size on the variations of green density in BJT test parts.
“[E]ngineers should measure the green density variation in the parts once the build design is fixed and use that for distortion compensation. If the build design is changed, say the location of parts or number of parts in the build is changed, the green density variation should be measured again.”
– Albert C. To, Department of Mechanical Engineering and Materials Science, Swanson School of Engineering, University of Pittsburgh
They found that spatial variations in BJT processes have a significant impact on green density, such that systems with larger build volumes were subject to notably higher discrepancies – more than 10%. Fortunately, by accounting for spatial green density variations in their finite element sintering models, the researchers were able to reduce the errors in predicting BJT part geometry to within 1% (approximately 0.5mm).
Balancing strength and ductility in Ti-6Al-4V alloys
Engineers from Pohang University of Science and Technology (POSTECH) and Korea Advanced Institute of Science and Technology (KAIST) have developed a new machine learning approach that optimizes Ti-6Al-4V alloys by adjusting the parameters of the laser powder bed fusion (L-PBF) process. Using a Pareto active learning framework, the researchers explored 296 candidate combinations – including both processing and post-processing parameters – based on an initial training dataset of 119 parameter combinations.
As a result, the team identified a set of ten Ti-6Al-4V alloys, with the best balance of strength and ductility exhibiting an ultimate tensile strength of 1,190 MPa and total elongation of 16.5%.
WAAM simulation
Wire arc additive manufacturing (WAAM) is often compared to conventional welding and, indeed, the two processes are quite similar. Nevertheless, there are crucial differences between conventional welding and WAAM and, as such, the latter is in need of process-specific data to ensure its optimal application. A team of researchers from Clausthal University of Technology in Germany did just that by applying thermal finite element simulations to compute the temperature evolution of WAAM components.
“Numerical simulations offer invaluable insights into the additive manufacturing process allowing for systematic analysis of various process parameters. When carefully calibrated with real experimental data, these simulations provide a reliable process model. This contrasts with traditional trial-and-error concepts or design of experiments, which often require numerous time-consuming and resource-intensive experiments, quickly becoming prohibitive when more parameters are involved. To optimize additive manufacturing processes effectively, numerical simulations and experimental validation should work in tandem.”
– Jendrik-Alexander Tröger, Institute of Applied Mechanics, Clausthal University of Technology
On the basis of experimental data, the researchers report that their simulations helped tune WAAM parameters to optimize component cooling, in addition to reducing processing time compared to manually selected parameters by nearly half.
Optimizing 3D printing for engineering plastics
One of the key advancements needed for polymer 3D printing to see more production applications is the ability to work with high-temperature plastics, such as polyether ether ketone (PEEK). That’s why a team of engineers from Hubei University of Technology and Huazhong University of Science and Technology in Wuhan, China has been studying how to optimize machine parameters for engineering plastics.
In their study, the researchers examined the effects of printing speed, layer thickness, and nozzle temperature – among others – on molding accuracy for PEEK samples. They found that layer thickness had the biggest influence on dimensional accuracy, followed by filling rate, nozzle temperature and printing speed. They report that the optimal combination of parameters for fused deposition modeling of PEEK is a printing speed of 15 mm/s, a layer thickness of 0.1 mm, a nozzle temperature of 420˚ C and a filling rate of 50%.
Additive manufacturing market matters
In this section, we discuss notable changes in the share prices of publicly traded additive manufacturing companies, with additional comments on major contracts and other announcements from both public and private companies. Note that these are subject to the latest available data as of January 31, 2025 at 9am EST.
Company | Ticker | Current Price | MoM % Change | YoY % Change |
3D Systems | DDD | $3.73 | 13.7 | -22.1 |
Desktop Metal | DM | $2.50 | 6.8 | -61.5 |
Markforged | MKFG | $2.90 | -7.6 | -57.2 |
Materialise | MTLS | $8.65 | 22.9 | 52.6 |
Nano Dimension | NNDM | $2.37 | -4.4 | -1.2 |
Stratasys | SSYS | $9.39 | 5.6 | -29.0 |
– | – | – | – | – |
Protolabs | PRLB | $42.00 | 7.4 | 16.4 |
Xometry | XMTR | $34.93 | -18.1 | 8.5 |
– | – | – | – | – |
S&P 500 | SPX | $6,071.17 | 3.2 | 25.3 |
Notable shifts in AM share price
Amongst the six publicly traded AM suppliers listed above, two in particular stand out in both month-over-month and year-over-year performance.
The first is 3D Systems, which saw the second largest positive shift month-over-month and the second smallest negative shift year-over-year. The company has made several important announcements since December, including the sale of its Geomagic software portfolio to Hexagon as well as a new collaboration with Daimler Truck | Daimler Buses on 3D printing spare parts.
The second publicly traded AM supplier worth noting is Materialise, which, in addition to having the largest positive shift month-over-month, is the only AM supplier to see a positive shift in share price year-over-year. As a 3D printing software provider, the company partnered with numerous organizations in 2024, including nTop Ansys and EOS, as well as Renishaw, Stratasys and ArcelorMittal. This co-opetitive approach was exemplified by the formation of the Leading Minds Consortium at last year’s Formnext.
Meanwhile, the two largest publicly traded AM service providers, Protolabs and Xometry, are a mixed bag. The former is up slightly month-over-month and more substantially year-over-year, while the latter is down significantly from December but still up compared to January 2024.
Overall, publicly traded AM companies are showing positive median performance month-over-month and, while they’re still in the negatives year-over-year, they’re down significantly less compared with their YoY performance of the past two years. This suggests that the burgeoning optimism for the AM industry’s future is well warranted.
AM business developments
A few other noteworthy events took place in the AM business world over the past month.
Let’s start with the good news.
EOS celebrated a significant milestone in January with the sale of its 5,000th industrial 3D printer: an EOS M 400-4. The machine was acquired by North Carolina-based Keselowski Advanced Manufacturing (KAM), which is part of contract manufacturer, ADDMAN Group. In an EOS press release about the sale, North American president Glynn Fletcher referred to the company’s founder, Hans Langer, saying:
“To this day, we remain true to Hans’ original vision. This focus ensures we dedicate all our energy to building the best quality products and services for organizations like ADDMAN, rather than bowing to deceptive market dynamics and misguided competitive pressures. For us, this has resulted in consistent business growth, and I’m confident we’ll reach 10,000 installations much faster than the first 100.”
Fletcher’s statement brings to mind the latest update from Nano Dimension, which dominated much of the AM industry news cycle last year with the announcement that it would acquire Desktop Metal after quashing Stratasys’ attempt to do the same in 2023. Not long after that came a second acquisition announcement from Nano Dimension, this time targeting Markforged. The company capped off last year’s drama with the ousting of CEO Yoav Stern but the situation has hardly stabilized since then.
This week, interim CEO Julien Lederman issued a statement to Nano Dimension’s shareholders, acknowledging the company’s “substantial negative enterprise value” and promising to prioritize shareholder interests, demonstrable return on investment (ROI) and “prudent operating expense management” (in that order). What that looks like so far is a decision to end Nano Dimension’s shareholder rights plan and a $150M stock buyback.
In light of this, claims from Nano Dimension’s previous leadership that the investment firms Murchison Ltd. and Anson Advisors Inc. were “try[ing] to distract our leadership team, liquidate Nano, and line their own pockets with our cash reserves,” may seem vindicated, hyperbole notwithstanding.
I can’t help but wonder whether Nano Dimension is starting down the path that many believe led to Boeing’s woes: prioritizing short-term financial gains for shareholders over long-term investments in engineering. If that is the case, we should expect Lederman (or his permanent replacement) to open the second envelope before the end of Q1.
3DPTV
You’ve made it this far, so here’s a little treat for the end of our first column.
Cody Clements is an Australian metal fabricator and automotive electrician who also hosts a YouTube channel called Stick Shift Garage. In one of his most recent videos, Clements tried forming sheet aluminum using 3D printed dies made from PLA+ and designed on Fusion 360.
The results are surprisingly good and his viewers’ responses were so enthusiastic that he just released a follow-up video where he puts some of their suggestions into practice. Both are worth watching if you’re interested in 3D printing for tooling applications.
That wraps up the first edition of our Additive Manufacturing Progress Update!
Send your questions, comments or complaints to me at [email protected], and they might just appear in next month’s column.