AACHEN, Germany, Dec 18, 2024 – ModuleWorks announces the 2024.12 release of its software components for digital manufacturing and digital factory. This latest release of the ModuleWorks SDK includes various new and enhanced features aimed at increasing safety, toolpath generation efficiency and part quality. These features contain enhancements across multiple components, ranging from multi-axis surface finishing to simulation and many more.
Multi-Axis Surface Finishing – SWARF Machining
Accurate 4-Axis SWARF Mode
The 4-axis SWARF mode has been significantly enhanced to achieve optimal geometric accuracy. This improvement addresses the challenge of machining complex surfaces, such as cylindrical cams, using flank milling on a cost-effective 4-axis machine. Traditionally, aligning the tool with the surfaces when using a tool smaller than the slot has been difficult. However, the new algorithm now accounts for kinematic limitations during the initial toolpath calculation, eliminating the need for 4-axis enforcement in post-processing and reducing the risk of inaccuracies.
With the ModuleWorks 2024.12 release, this enhancement brings several benefits, including improved accuracy of parts, reduced machining costs and greater flexibility in selecting tool diameters. By addressing these challenges, the new 4-axis SWARF mode enhances precision and cost-effectiveness in machining, making it a valuable upgrade for manufacturers.
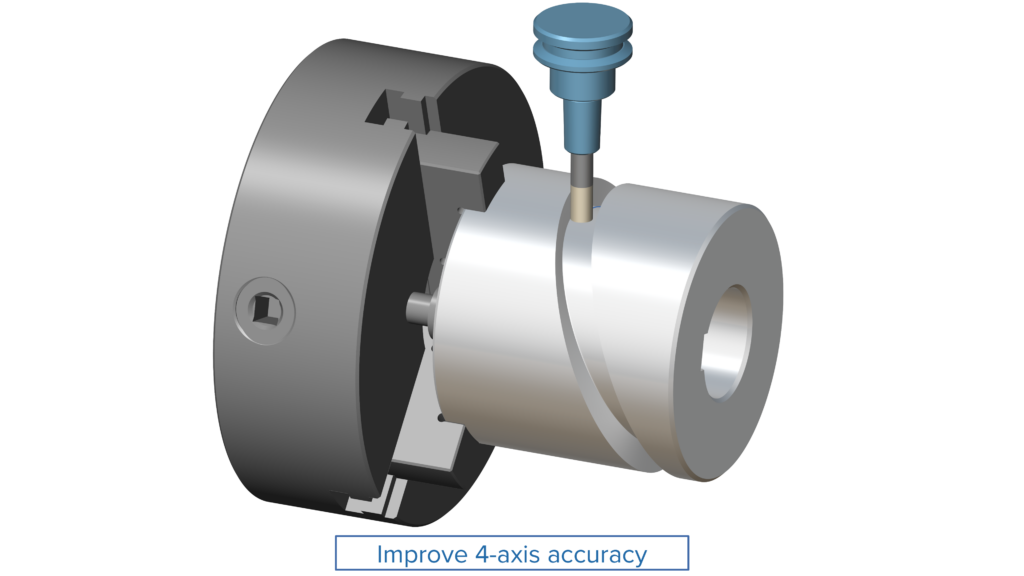
Multi-Axis Edge Finishing – Deburring
Consolidated 3+2 Behaviour
Until now, it was difficult for users to eliminate all the simultaneous 5-axis moves from a 3+2-axis deburring toolpath. This would result in unpredictable motion on the machine tool during operation.
In the 2024.12 release, 3+2-axis deburring has been improved to provide 3+2 orientation with minimum 5-axis motion. As a result, users benefit from enhanced machining safety and accuracy.
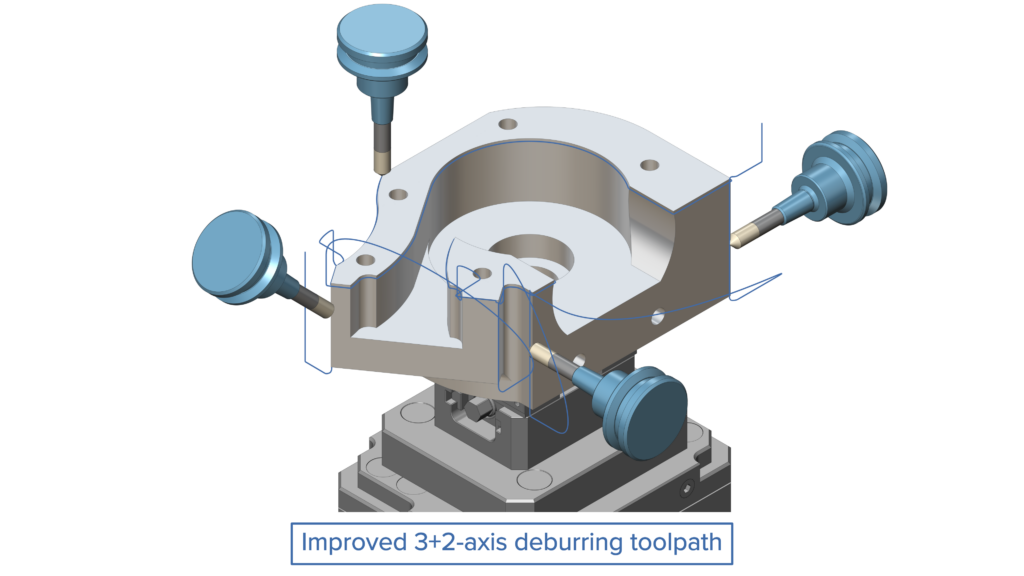
3-Axis Machining
Automatic Machining Area for Barrel Tools
During 3-axis finishing, users often struggle to manually identify and define the areas that can be machined by the different sections of the barrel tools. This can result in significant increases in both programming and machining cycle times.
A new feature in ModuleWorks 2024.12 assists users by automatically identifying the steep and shallow areas on the part. This enables optimal use of the range of barrel tools, reducing cycle times for finishing and improving surface quality.

Rest Finish Based on Previous Tool Shaft Length
In previous releases, creating a rest finish operation with a long tool was difficult when the part had been partially machined using the same tool with a shorter stick-out.
The ModuleWorks 2024.12 release introduces a new option that automatically detects the areas left by the previous short tool. This enables efficient machining with a longer tool stick-out. It assists users by automatically detecting the rest regions. Users can also apply more specific cutting conditions to each operation to improve the surface quality.

Simulation SDK – Cutting Simulation
New Graph-Based Triangulation
Users often struggle to achieve optimal triangulation due to the need to balance performance and stock quality. For very large and complex stock models, simulation responsiveness can be poor, leading to significant delays on the shop floor.
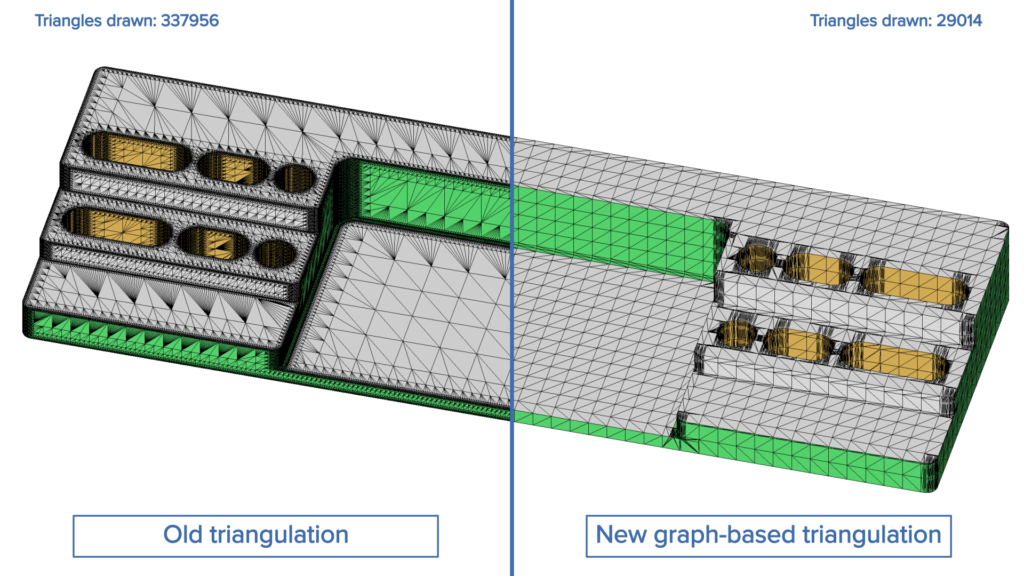
The ModuleWorks 2024.12 release solves this problem through a new triangulation method based on a dexel model. This new method delivers significantly faster stock drawing and mesh exports, resulting in improved simulation performance. In addition, the new triangulation improves the watertightness of exported meshes.
ModuleWorks 2024.12 is available for download from the ModuleWorks website.