This transformative technology opens new worlds for product design and beyond. Here’s how it works and how to get started.
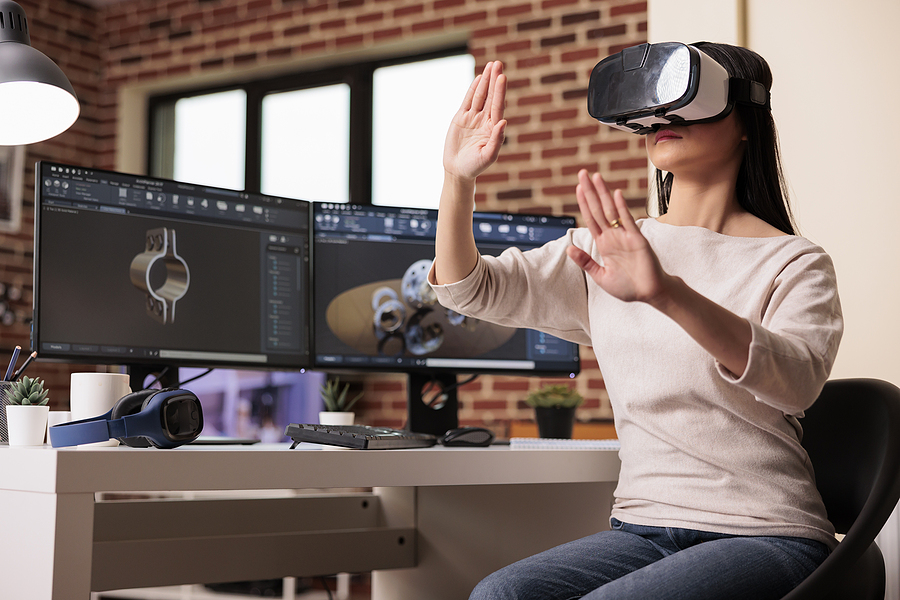
Virtual reality (VR) is opening new worlds for engineers.
The impressive technology has come far in the past few decades of research and development. Today, users can strap on a head-mounted display (HMD) and enter a virtual world that looks strikingly realistic—or fantastically alien. The possibilities of VR are wide open, but it’s already proving to be a practical and versatile tool for engineering and manufacturing professionals.
What is virtual reality (VR)?
Virtual reality represents one extreme of the virtuality continuum, the theoretical framework underpinning spatial computing. It’s balanced on the other side by reality (real reality, if you like), and the two poles are bridged by mixed reality technologies such as augmented reality.
VR immerses the user in a simulated, computer generated world. The computer is (or is connected to) a head-mounted display (HMD), a special headset with two screens, one for each of the wearer’s eyes. Using the same principal as 3D movie glasses, each screen shows the user a slightly different image to create the illusion of depth in the simulated world.
This illusion can be incredibly effective. A high-end HMD and well-made virtual environment can convince the user that he or she is really in another place (the genre of horror VR games demonstrates this well—you can easily find footage of players ripping off their headsets when the game starts to feel a little too real).

How do users interact with a virtual world? Most VR applications are controlled with one or two hand controllers held by the user. The motion of these controllers is tracked and often represented in VR with a laser-like beam that can point at elements in the VR world. To move through the world, there are two common approaches: users either push a button on the controller to “walk” forward or simply point and click to teleport to a new spot.
Some VR headsets track the user’s eye and hand movements and use glances and gestures to interact with the application. For an even more immersive experience, omnidirectional treadmills allow users to physically walk through the virtual environment.
None of these control methods have emerged as a clear standard, so the user interface for virtual reality will likely continue to evolve along with VR hardware and software.
How are engineers using virtual reality?
As with augmented reality, engineers can use virtual reality to get up close and personal with their designs. Rather than spinning a 3D model in a CAD program, engineers can put on a VR headset and see the same model in a virtual world. They could walk around it to see it from different angles and in true-to-life size. They could even hide parts, adjust materials, explode the assembly or examine section views—not on a flat computer screen, but in immersive virtual world.
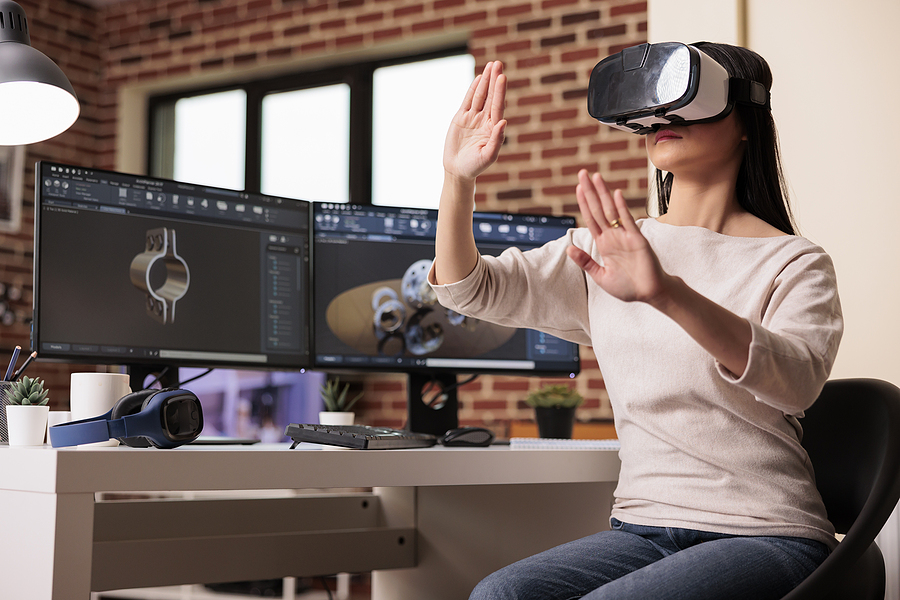
VR headsets with eye tracking allow engineers to evaluate how users would interact with a design. For example, engineers designing the layout for an airplane cockpit could learn where the pilot’s eyes are most drawn and optimize the design accordingly. Similarly, VR can help designers optimize the ergonomics of a human-operated machine by revealing how test users interact with the virtual model.
VR can also serve as a virtual meeting space for collaborative design. Engineers from anywhere in the world could put on a headset and join their colleagues in reviewing a model, no long-haul flights required. Think of it like a three dimensional Zoom meeting with the 3D equivalent of screen sharing.
The same idea is used in the architecture, engineering and construction (AEC) industry to walk through virtual buildings. Architects, engineers, clients and other stakeholders can use VR to get a spatially accurate feel for a design before it’s built. This is a far leap beyond reviewing architectural drawings and renderings. As with engineering design reviews, the immersivity of VR is what adds immeasurable value.
How engineers can get started with virtual reality
You can’t visit virtual reality without a VR headset, but there are plenty of options to choose from. These range from consumer-targeted products for a few hundred dollars to enterprise VR headsets that provide better resolution and responsiveness but cost thousands of dollars. Some VR headsets are self-contained computers with internal processors, while others depend on a connection to a GPU-equipped engineering workstation.
There’s plenty of software for engineering users of VR. Some CAD programs support VR directly, allowing designers to easily switch to a virtual view of their models. Other software caters to VR design reviews with features for collaboration and markup. Game engine software, sometimes called real-time 3D software, can be used to develop custom VR experiences using existing CAD models.
Though there’s an upfront cost to getting started with VR—both in the price of VR headsets and software as well as the learning curve for users—for many engineers, the cost is well worth it. VR provides an unparalleled way to visualize and refine a design, and has thus become an integral part of many engineering workflows.